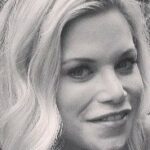
A pick list, or picking list, directs warehouse workers to certain items and specific quantities to gather or “pick” to complete an order. Pick lists enhance efficiency in the order fulfillment process by clearly communicating to workers which items need to be retrieved from inventory to assemble customer orders.
Pick lists help streamline warehouse operations by eliminating guesswork so workers know exactly which products to pick and how many of them to pick for each order. In the world of warehousing and distribution, the humble pick list is a key, behind-the-scenes player in getting products into the hands of customers.
Here’s everything to know about how a pick list works in order fulfillment and why they are so important for warehouses.
How Does a Pick List Work?
A pick list is a document that guides warehouse workers to locate and retrieve, or ” pick“, the correct items to fulfill customer orders. When it comes to understanding what is a pick list, it can be helpful to start by visualizing how the entire order fulfillment process works.
It starts when an order comes into the warehouse. Warehouse management software will analyze inventory data and create a custom pick list for the order. This pick list outlines important information, such as exactly which items need to be picked, how many of each item, and their exact locations in the warehouse.
Equipped with this pick list, warehouse employees, or “pickers” will go out about the warehouse to locate the shelves, bins, or pallet spots where the items live. They follow the list step-by-step, using barcode scanners to confirm each item as it’s picked by scanning product barcodes and serial numbers.
The pick list not only guides what’s known as the order-picking process but also helps workers assemble the right quantity of each item needed to fulfill the customer’s order. In this way, warehouses can boost accuracy and limit order processing errors that could happen if workers had to guess how many of each item to include.
The pick list serves its purpose by ensuring warehouse workers move quickly through the warehouse to locate and pick the exact assortment of items required to complete the order. Once all items are picked, the order is moved to packing and shipping.
2 Types of Pick Lists
Before tablets and smartphones, there was only one type of picking list, but now there are two:
1. Physical Document Pick Lists
A physical pick list was the only way to fill orders for decades. Employees would carry clipboards and check off items as they grabbed them. This could be a slow and inaccurate process. Once items were picked, the physical pick list would have to be analyzed and subtracted from the documented inventory of the warehouse.
2. Digital Pick Lists
In the 21st century, most pick lists have gone digital. Employees carry digital devices that have the picking list tied to a warehouse management system (WMS). The item SKUs are listed along with pictures and quantities of the various items needed.
As the employee picks an item they can check it off in the interface. Because the software is tied to the WMS, real-time inventory tracking is possible. Digital pick lists reduce picking time, save money, and increase order accuracy.
4 Methods for Grouping a Pick List
Of course, once the employees have the pick list in hand, they still have to figure out how they’ll get the items. Picking items needs to be an organized process and is usually determined by the size of the warehouse.
Generally, employees should pick items based on location to limit how much time they spend walking around. Here are a couple methods for how to effectively group a pick list.
1. Pick-to-Order
As orders come in, employees retrieve the items. Once that order’s picked, they move on to the next. This method works fine when orders are few and far between, but once orders increase, it becomes far too time-consuming.
2. Batch Picking
By picking multiple orders at once, employees can retrieve items in one location before moving on to the next. If they need five of the same kind of shirt for five different orders, it makes sense to pick all five in one go.
3. Zone Picking
Zone picking is an “assembly line” style. Rather than one picker moving through an entire warehouse, multiple employees work in different zones. Each employee is responsible for one part of an order so picking can be done simultaneously.
4. Wave Picking
For the largest warehouses, wave picking is the fastest method. Workers will pick batches of items in their zone and send the batches to the next zones. The orders move through in “waves” for ultimate efficiency.
Example of a Pick List
So what is a pick list? Let’s say you were responsible for assembling orders in a warehouse. You’d get a pick list with information like this:
Item SKU / Item Description / Warehouse Location / Amount Required
————————————————————–
| Pick List |
————————————————————–
| Order Number: 12345 Date: 2024-02-08 |
————————————————————–
| Item SKU | Description | Quantity | Location |
————————————————————–
| 101 | Widget A | 2 | A-23 |
| 205 | Gadget B | 1 | B-15 |
| 310 | Gizmo C | 3 | C-08 |
| 152 | Thingamajig D | 4 | D-04 |
————————————————————–
| Total Items: 4 |
————————————————————–
| Prepared by: Print Bind Ship |
————————————————————–
These categories would be in a spreadsheet format for easy, at-a-glance reading. At the bottom would be the total number of items required so you could check against how many you’ve picked overall. The list might also contain bar codes for automatic checking.
7 Steps for How to Create a Pick List
Here are seven steps to follow when assembling a pick list.
Step 1: Customer Information
Pickers don’t need to know customer information, but a physical list will be handed off to packers and labelers who will need that information. Digital picking lists are more segmented by job, so pickers who are using tablets or phones will probably never see the customer info.
Step 2: Date and Time of Order
Because so many online businesses offer “two-day shipping” or “same-day shipping,” the date and time of the order give pickers an idea of how quickly the orders need to be fulfilled. They also help pickers prioritize which order should get picked first.
Step 3: Order Number
If there’s an issue with the shipment, the order number is essential for the customer to get the order corrected. Order numbers make internal tracking easier and more transparent.
Step 4: Product Location in Warehouse
For facilities that use robots to bring shelves of goods directly to pickers, this is less important. For pickers who walk through the warehouse to find the goods, product location is essential. Warehouses need signs that clearly identify where and what the goods are.
Step 5: Order Quantity
Pickers need to be aware of how many of each item to grab. Someone might order five boxes of light bulbs. If a picker just grabs one box, they’re literally leaving a customer in the dark.
Step 6: Product SKUs
The stock-keeping unit, or SKU, is specific to every product and is never duplicated. Barcodes and digital lists make this process much simpler, but the picker still needs to make sure they’re grabbing the correct item.
Step 7: Description or Photo of the Product
To add another layer of protection against wrong orders, each item on the pick list should have a description and a photo. That way the employee knows they have the correct item.
Bypass the Pick List: Let Print Bind Ship Do It for You!
As an eCommerce brand, managing your order fulfillment in-house can quickly become overwhelming. Even if you have enough warehouse space and a dedicated warehouse management system, your businesses may quickly run into issues when it comes to trying to scale.
It can be a much smarter move to outsource your order fulfillment entirely to an expert like Print Bind Ship. As a dedicated fulfillment partner, Print Bind Ship has over 60 years of experience helping businesses with order processing, fulfillment, shipping logistics, customer returns, and more.
We operate some of the top-tier warehouse management systems on the market to ensure we get every order right. Our solutions can help you maintain customer satisfaction with accurate order fulfillment and timely shipping. And that’s not all, we also offer printing services to help you create print-on-demand books, merchandise, packaging, and even gift boxes for your brand. Learn more here.
When you trust Print Bind Ship with keeping your inventory and picking, packing, and shipping orders, you get the peace of mind that your customers will get exactly what they want. Make eCommerce easy — get in touch with the experts at Print Bind Ship for a free consultation!
FAQ
A pick list typically includes detailed product information such as SKUs or item numbers, product descriptions, storage locations like aisle number, section, level, and bin number, the required quantity to pick, and an area for the picker to acknowledge the pick with a confirmation scan or signature after retrieving the items.
By providing all required information to complete order fulfillment in an organized, step-by-step manner, pick lists eliminate the need for warehouse pickers to figure out for themselves where items are located or how many they need. This saves time, reduces walking to find items, minimizes picking errors, and allows the warehouse team to fulfill more orders reliably.
Yes, many Warehouse Management Systems (WMS) and inventory management software platforms will integrate with the order processing system to auto-generate pick lists. This allows details like SKUs, locations, and quantities to auto-populate for efficient picking. These systems also allow printing, exporting, or transferring digital pick lists to physical documents and handheld barcode scanners which warehouse personnel to complete picking.
A pick list is a document or digital list that guides warehouse workers through the picking process, detailing the specific items, quantities, and locations to be retrieved from inventory to fulfill customer orders.
Dropdowns are used in software interfaces, while picklists are physical or digital documents used in the warehouse picking workflow. Picklists are comprehensive lists of items and their respective storage locations that need to be physically picked and consolidated for order fulfillment.